Overmolding is a critical process in the manufacturing of cable assemblies, offering both aesthetic and functional benefits. It involves the use of a secondary injection molding process to add an additional layer of material over an existing part, typically a cable or connector. This process is used to enhance the durability, performance, and appearance of the cable assembly, making it more suitable for a variety of applications.
Understanding the intricacies of overmolding in cable assembly requires a deep dive into the process, materials used, benefits, applications, and potential challenges. This comprehensive glossary entry aims to provide a detailed explanation of overmolding in the context of cable assembly, breaking down each aspect to ensure a thorough understanding of this pivotal manufacturing process.
Process of Overmolding
The process of overmolding involves two primary stages: insert molding and overmolding. Insert molding is the initial stage where the cable and connector are assembled. The assembled parts are then placed into the overmolding machine, where they are subjected to the overmolding process.
The overmolding process begins with the heating of the thermoplastic material until it reaches a liquid state. The molten material is then injected into a mold cavity that encases the cable assembly. Once the material cools and solidifies, it forms a protective layer around the cable assembly, enhancing its durability and functionality.
Insert Molding
Insert molding is the first step in the overmolding process. It involves the assembly of the cable and connector, which are then placed into the mold. The purpose of this stage is to prepare the cable assembly for the overmolding process, ensuring that it is properly positioned within the mold.
During insert molding, the cable and connector are assembled manually or using automated equipment. The assembled parts are then placed into the mold, ensuring that they are properly aligned with the mold cavity. This is a critical step as it determines the accuracy and quality of the overmolded cable assembly.
Overmolding Stage
The overmolding stage is where the actual overmolding process takes place. The thermoplastic material is heated until it reaches a liquid state, and then injected into the mold cavity. The molten material encases the cable assembly, forming a protective layer once it cools and solidifies.
The overmolding stage requires precise control of the temperature and pressure to ensure that the molten material fills the mold cavity completely and evenly. This is crucial for achieving a high-quality overmolded cable assembly with enhanced durability and functionality.
Materials Used in Overmolding
Various materials can be used in the overmolding process, each offering unique properties and benefits. The choice of material depends on the application requirements of the cable assembly. Common materials used in overmolding include thermoplastic rubber (TPR), polyvinyl chloride (PVC), and thermoplastic elastomers (TPE).
TPR is a versatile material that offers excellent flexibility and durability. It is resistant to abrasion and impact, making it ideal for applications that require a high level of durability. PVC is a cost-effective material that offers good electrical insulation properties. It is commonly used in applications that require a high level of electrical insulation. TPE is a flexible and durable material that offers excellent resistance to environmental factors such as UV radiation and ozone. It is commonly used in outdoor applications due to its excellent weather resistance.
Thermoplastic Rubber (TPR)
Thermoplastic rubber (TPR) is a type of thermoplastic elastomer that combines the properties of rubber with the processability of plastics. It offers excellent flexibility and durability, making it ideal for overmolding applications. TPR is resistant to abrasion and impact, which enhances the durability of the cable assembly.
TPR is also resistant to a wide range of chemicals, making it suitable for applications that involve exposure to harsh chemicals. It can withstand high temperatures, making it ideal for applications that involve exposure to heat. Furthermore, TPR can be easily colored, allowing for the production of cable assemblies in a variety of colors.
Polyvinyl Chloride (PVC)
Polyvinyl chloride (PVC) is a widely used thermoplastic material that offers good electrical insulation properties. It is a cost-effective material that is easy to process, making it a popular choice for overmolding applications. PVC can be used to enhance the electrical insulation of the cable assembly, improving its safety and performance.
PVC is resistant to oxidation and corrosion, making it suitable for applications that involve exposure to harsh environmental conditions. It can withstand a wide range of temperatures, making it suitable for applications that involve exposure to heat or cold. Furthermore, PVC can be easily colored, allowing for the production of cable assemblies in a variety of colors.
Thermoplastic Elastomers (TPE)
Thermoplastic elastomers (TPE) are a type of thermoplastic material that combines the properties of elastomers with the processability of plastics. They offer excellent flexibility and durability, making them ideal for overmolding applications. TPEs are resistant to environmental factors such as UV radiation and ozone, making them suitable for outdoor applications.
TPEs are also resistant to a wide range of chemicals, making them suitable for applications that involve exposure to harsh chemicals. They can withstand high temperatures, making them ideal for applications that involve exposure to heat. Furthermore, TPEs can be easily colored, allowing for the production of cable assemblies in a variety of colors.
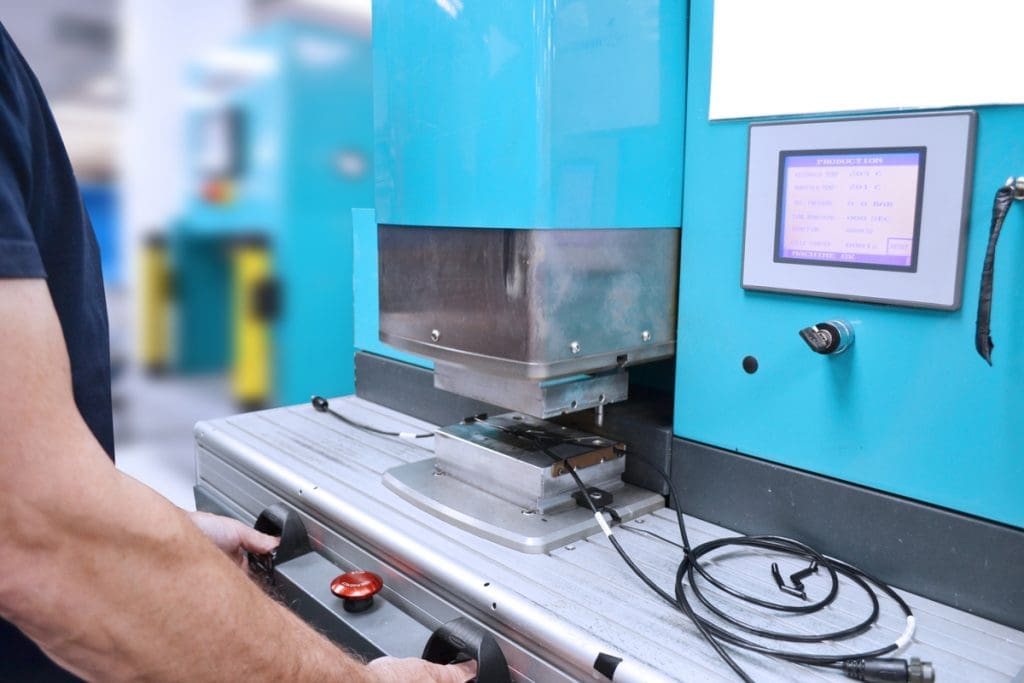
Benefits of Overmolding
Overmolding offers several benefits that enhance the performance, durability, and appearance of the cable assembly. These benefits include improved strain relief, enhanced durability, increased performance, improved aesthetics, and added functionality.
Improved strain relief is one of the key benefits of overmolding. The overmolded material provides a protective layer that absorbs and distributes the forces exerted on the cable assembly, reducing the strain on the cable and connector. This enhances the durability and lifespan of the cable assembly.
Enhanced Durability
The overmolded material forms a protective layer around the cable assembly, enhancing its durability. The material is resistant to abrasion, impact, and environmental factors, protecting the cable assembly from damage. This enhances the lifespan of the cable assembly, reducing the need for frequent replacements.
Furthermore, the overmolded material provides additional structural support to the cable assembly, reducing the risk of mechanical failure. This is particularly beneficial in applications that involve high levels of mechanical stress, such as industrial and automotive applications.
Increased Performance
Overmolding can enhance the performance of the cable assembly by improving its electrical insulation and signal integrity. The overmolded material provides a barrier that prevents electrical interference, improving the signal quality. This is particularly beneficial in applications that involve high-speed data transmission, such as telecommunications and computing.
Furthermore, the overmolded material can improve the thermal management of the cable assembly, enhancing its performance in high-temperature applications. The material can absorb and dissipate heat, preventing overheating and improving the reliability of the cable assembly.
Improved Aesthetics
Overmolding can enhance the aesthetics of the cable assembly by providing a smooth, seamless finish. The overmolded material can be colored and textured, allowing for the production of cable assemblies in a variety of designs and styles. This is particularly beneficial in consumer electronics, where aesthetics play a key role in product appeal.
Furthermore, overmolding can hide imperfections in the cable assembly, such as weld lines and parting lines. This results in a high-quality finish that enhances the overall appearance of the cable assembly.
Added Functionality
Overmolding can add functionality to the cable assembly by incorporating additional features into the overmolded material. These features can include grips, seals, and grommets, which enhance the usability and functionality of the cable assembly.
For example, grips can enhance the handling and usability of the cable assembly, making it easier to connect and disconnect. Seals can enhance the environmental resistance of the cable assembly, protecting it from moisture and dust. Grommets can enhance the strain relief of the cable assembly, reducing the strain on the cable and connector.
Applications of Overmolding
Overmolding is used in a wide range of applications, from consumer electronics to industrial machinery. The process enhances the performance, durability, and appearance of the cable assembly, making it suitable for a variety of applications.
Consumer electronics is one of the main applications of overmolding. The process is used to produce cable assemblies for devices such as smartphones, tablets, and laptops. The overmolded material enhances the durability and performance of the cable assembly, while also improving its aesthetics.
Industrial Applications
Overmolding is widely used in industrial applications, where the durability and performance of the cable assembly are critical. The process is used to produce cable assemblies for machinery and equipment used in industries such as manufacturing, construction, and transportation.
The overmolded material enhances the durability of the cable assembly, protecting it from mechanical stress and environmental factors. It also improves the performance of the cable assembly, enhancing its electrical insulation and signal integrity. This ensures reliable operation of the machinery and equipment, improving productivity and efficiency.
Medical Applications
Overmolding is also used in medical applications, where the safety and performance of the cable assembly are paramount. The process is used to produce cable assemblies for medical devices such as diagnostic equipment, surgical instruments, and patient monitoring systems.
The overmolded material enhances the safety of the cable assembly by providing electrical insulation and strain relief. It also improves the performance of the cable assembly, ensuring reliable data transmission. This ensures accurate diagnosis and treatment, improving patient outcomes.
Automotive Applications
Overmolding is used in automotive applications, where the durability and performance of the cable assembly are critical. The process is used to produce cable assemblies for vehicles, enhancing their performance and reliability.
The overmolded material enhances the durability of the cable assembly, protecting it from mechanical stress and environmental factors. It also improves the performance of the cable assembly, enhancing its electrical insulation and signal integrity. This ensures reliable operation of the vehicle, improving safety and performance.

Challenges in Overmolding
While overmolding offers numerous benefits, it also presents several challenges. These challenges include material selection, mold design, process control, and cost. Understanding these challenges is crucial for achieving a successful overmolding process.
Material selection is a critical challenge in overmolding. The material must be compatible with the cable and connector, and meet the application requirements of the cable assembly. The material must also be suitable for the overmolding process, ensuring a high-quality overmolded cable assembly.
Mold Design
Mold design is another critical challenge in overmolding. The mold must be designed to accommodate the cable assembly and the overmolding material. The mold must also be designed to ensure accurate and even filling of the mold cavity, ensuring a high-quality overmolded cable assembly.
The design of the mold is influenced by several factors, including the size and shape of the cable assembly, the properties of the overmolding material, and the requirements of the overmolding process. This requires a thorough understanding of mold design principles and practices, as well as the specific requirements of the overmolding process.
Process Control
Process control is a key challenge in overmolding. The overmolding process requires precise control of the temperature and pressure to ensure that the molten material fills the mold cavity completely and evenly. This is crucial for achieving a high-quality overmolded cable assembly.
Process control is influenced by several factors, including the properties of the overmolding material, the design of the mold, and the requirements of the overmolding machine. This requires a thorough understanding of process control principles and practices, as well as the specific requirements of the overmolding process.
Cost
Cost is a significant challenge in overmolding. The process involves the use of expensive materials and equipment, as well as a high level of expertise. This can make overmolding a costly process, particularly for small-scale production.
However, the benefits of overmolding often outweigh the costs. The process enhances the performance, durability, and appearance of the cable assembly, making it more suitable for a variety of applications. This can result in a higher return on investment, offsetting the costs of the overmolding process.
Conclusion
Overmolding is a critical process in the manufacturing of cable assemblies, offering both aesthetic and functional benefits. It involves the use of a secondary injection molding process to add an additional layer of material over an existing part, typically a cable or connector. This process is used to enhance the durability, performance, and appearance of the cable assembly, making it more suitable for a variety of applications.
Understanding the intricacies of overmolding in cable assembly requires a deep dive into the process, materials used, benefits, applications, and potential challenges. This comprehensive glossary entry aims to provide a detailed explanation of overmolding in the context of cable assembly, breaking down each aspect to ensure a thorough understanding of this pivotal manufacturing process.
Ready to enhance your cable assemblies with the proven benefits of overmolding? Cornelius Electronics, with over four decades of expertise in contract manufacturing, is here to elevate your products. Our UK-based facility is equipped to deliver high-quality, partnership-focused solutions tailored to your needs. Don’t compromise on durability and performance. Get in touch with us today and let us help you achieve excellence in your cable assembly requirements.